Introduction
Industry 4.0 is a new way to meet the demands of increasingly demanding consumers. This is called being Consumer Centric.
This Industry 4.0, also called the industry of the future, allows to assess, design and organize production tools in a completely new way by pushing back the limits of the traditional industry thanks to automation, real-time data processing, machine learning, etc…
The central element of this new version of the industry is data. “Data” is all the information collected by the various sensors and elements installed on the production lines. Once collected and processed, the data allows companies to improve their various production processes.
For several years now, robotics has been evolving and developing in the industry. Expensive and not very flexible, traditional robots however allow to accomplish a set of physical and repetitive tasks that cause MSD among employees, while significantly increasing the output on the production line.
More recently, major developments in robotics have taken place within the industry. Indeed, collaborative robotics, also known as cobotics, has appeared in order to meet the new expectations of companies.
The application of cobot in industry 4.0
The cobot is at the heart of this fourth industrial revolution. While robotics first appeared in factories a long time ago, collaborative robotics arrived in the industry recently.
This technology has therefore developed in parallel with traditional robotics in order to meet needs that the latter could not meet.
- The problem of ease of access:
Traditional industrial robots were created to improve the speed and efficiency of a production line.
Installed at a precise location on the production line, they are intended to remain there. Their programming is therefore done in such a way that the robot performs only its tasks, quickly and continuously. If the company wishes to make the robot perform another task, the robot program will have to be completely rewritten and moved to another location. This method is very time-consuming, expensive and difficult to implement.
The name “collaborative robot” implies a collaboration between the robot and the human. Beyond the physical interaction on the same production line, in a simultaneous way, between a robot and a human, the collaborative robot is also created to be accessible to the greatest number in terms of use.
Collaborative robots thus allow operators to act directly, according to the immediate needs of the company, on the tasks performed by the robot. It is therefore a real complementarity of roles between operators and robots.
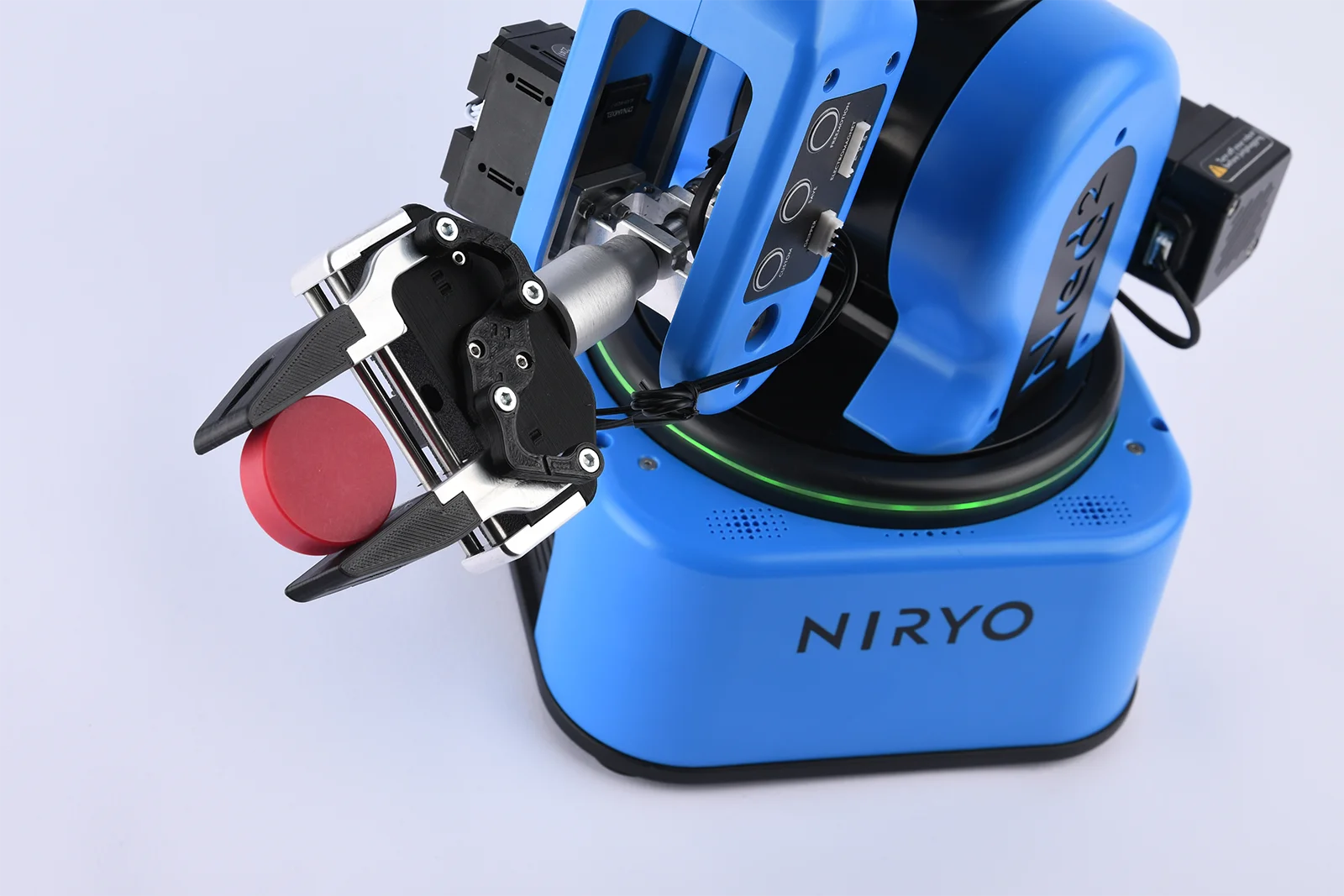
- The problem of agility:
As previously mentioned, traditional industrial robots are very inflexible. In addition to the complexity of a total redesign of the robot program, its weight and size make it very inflexible. It is intended to remain at the location decided upon during its first installation.
In addition to the lack of flexibility, the installation of a traditional industrial robot is very expensive because of the required layout and redesign of the production lines. In addition to this, the size of the robot, as well as its safety perimeter requires a large amount of space.

Contrary to traditional robots, collaborative robots are created to offer flexibility to the company according to its needs. First of all, they are much lighter and smaller. It is therefore much simpler to move a cobot along the production line.
In addition to its practicality, the collaborative robot is programmed to bring flexibility to companies. It is possible to modify what the robot needs to do in a very simple way, requiring no programming or robotics knowledge.
It is thus possible to meet different needs in a punctual way with a single collaborative robot, in a much more practical, fast and above all much less expensive way than with a traditional industrial robot.
- The problem of security:
Traditional industrial robots were created to take the place of operators at certain levels of the production line in order to reduce employee health problems and to increase production rates. In order to reach a high rate, the robot must perform fast movements, which are sometimes dangerous.
These fast movements represent a real danger for the surrounding people. Conventional robots are not equipped with special sensors, they do not detect the presence of a human in close proximity and can be the cause of incidents. This is why traditional robots are surrounded by cages so that no one is allowed in the intervention area around the robot.
The cobots are created to interact intelligently with humans. Equipped with sensors to stop the robot in case of unwanted contact with an external element, manufactured with much lighter and rounded frames, they are much safer for the operators and help to secure the working environment of operators. The speed and power of the cobots is also controlled and governed by safety standards so as not to pose any danger to the operators.
- The problem of cost:
The first incentive for buying an industrial robot or a collaborative robot is the search for an increase in productivity. This incentive is particularly justified when buying a traditional industrial robot because it increases the rate at which tasks are performed and the precision with which they are carried out.
However, industrial robots are extremely expensive and the return on investment for the purchase of an industrial robot can be calculated over many years. They are therefore difficult to access for small and medium-sized companies, especially since they do not meet all needs (lack of agility, concentration on a single product …).
Collaborative robots, also called cobots, are much more accessible than traditional robots. Indeed, the cost of a cobot is much lower than a traditional robot, both financially and in terms of the allocation of space and time to be devoted to deployment. This allows collaborative robots to optimize the ROI, making it particularly attractive to companies.
The cobot at the heart of the improvement process
The reasons mentioned above are not the only reasons why cobots are at the heart of Industry 4.0.
Another difference between traditional robots and cobots is the fact that the latter are connected. The IoT, the Internet of Things, is at the heart of how collaborative robots work (we call it IoRT, Internet of Robotic Things.)
Equipped with sensors, they offer companies global visibility of the elements within their factory, at all levels. The information is available at the level of the sensors, but also at the level of the cobots, the production line, and even at the level of the entire factory.
Collaborative robots can be equipped with a whole set of sensors that generate a multitude of relevant data: sensors for position, motor temperature, torques, collisions, vibrations, etc.
The information collected by the equipment on the cobots needs to be processed. Indeed, it is important to analyze the information obtained in order to propose improvements to the production process in order to increase productivity and efficiency.
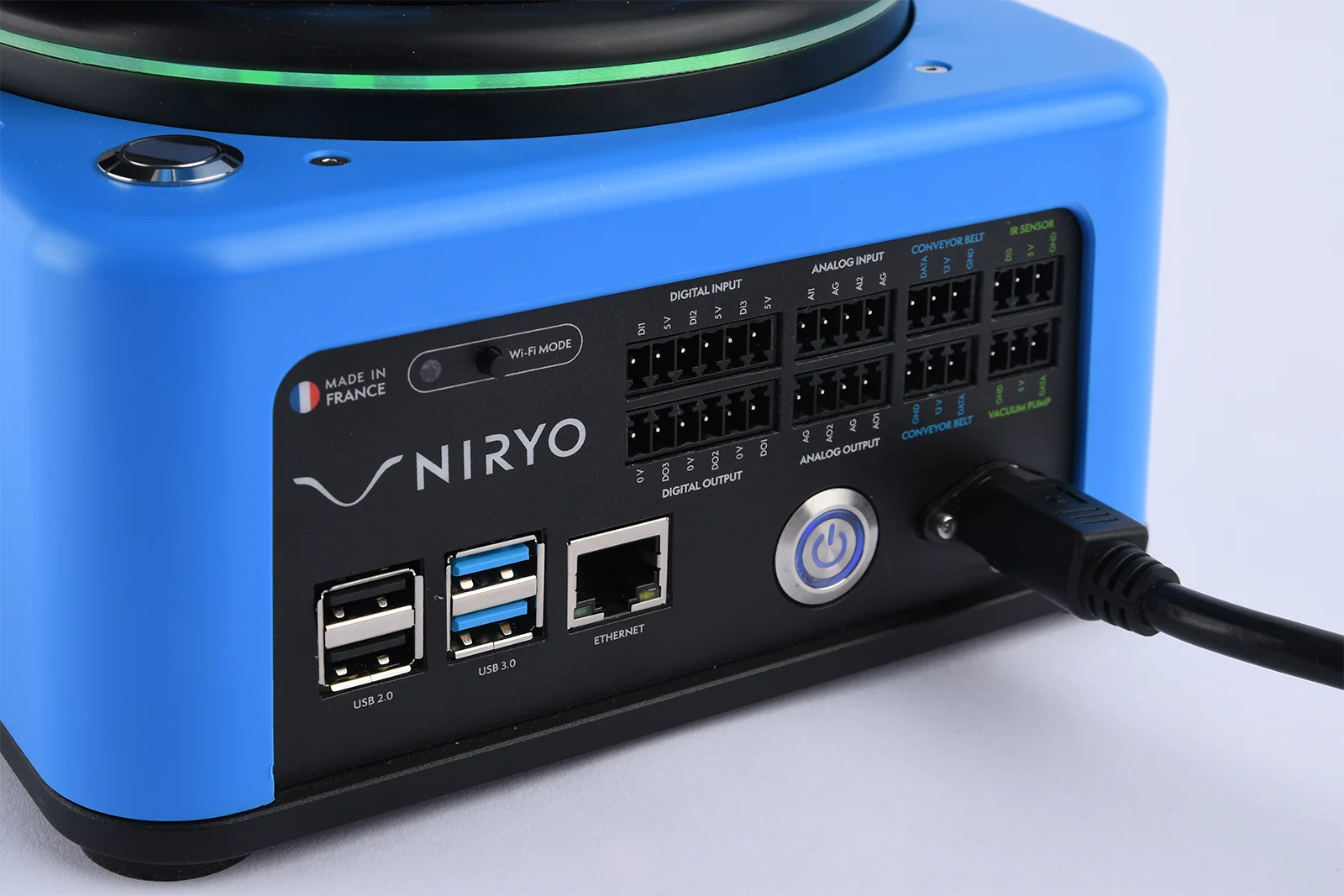
The information (the data) obtained allows to measure the key performance indexes of the production process, thus detecting malfunctions, weaknesses and allowing the implementation of a predictive maintenance system. This makes it possible to anticipate breakdowns, to know the origin of weaknesses in the production process, to ensure that machines are correctly calibrated for optimal use, to anticipate maintenance cycles and to intervene physically whenever necessary.
This information also helps to inform the teams about the overall productivity of the production line.
All the information obtained from the sensors on the cobots can be incorporated into the ROI calculation.
Conclusion
Changes in consumption are therefore at the very origin of the fourth industrial revolution. Indeed, consumers have more and more precise desires, tailor-made products requiring a significant expansion of the references proposed by companies. Seasonality is also an element which is increasingly taken into account by consumers.
It is therefore essential for companies to turn to a consumer centric production, in order to best respond to the needs of consumers who change with the seasons and over the years.
If traditional robots still deserve their place in the industry, even the industry of the future, cobots are the first technological pillar of this industry of the future, allowing companies to continue to meet consumer demands in real time by adapting their production process with flexible and agile tools.